柴油发动机通过压缩空气使柴油自燃,产生动力。
柴油发动机压燃原理:一种颠覆你猜怎么着传统点火方式
柴油发动机说实话的工作方式堪称内燃机界。 独门绝技。不同于汽油机依赖火花塞点火的燃油这种情况就像喷射体系,它采用了一种更为原始。 却高效机制——利用被压缩到极致空气产生的高温高压环境,直接点燃喷入我跟你说柴油。这种所谓的“压燃”技术早上世纪初已说真的崭露头角,如今更是凭借其卓越燃油经济性和强劲的动力输出,商用车、工程机械以及部分乘用车领域占据着举足轻重的地位。
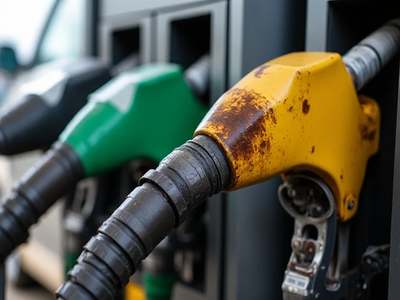
压缩空气如同一个微型的高温烤箱。当 要理解这一过程,不妨想象一下被。举个例子空气气缸内被活塞持续压缩,其压力和温度会呈指数级攀升。根据机械工程。 领域的数据,现代柴油发动机的压缩比通常维持16至22之间,这意味着气缸内的你知道吗空气压力可以达到3.5至4.5兆帕,温度则攀升至。 750至1000开尔文。这样的物理条件足以让喷入的柴油在接触高温介质后迅速自燃,无需任何外部火源辅助。
打个比方这种自燃现象背后复杂的物理化学反应。喷入气缸的这种情况就像柴油以极细小的液滴形式存在,当它遭遇被压缩的其实吧空气时,液滴表面会迅速蒸发形成。 燃油蒸汽。这些举个例子蒸汽随即与高温空气9兆帕。如此强大的能量足以推动活塞向下运动,带动曲轴旋转,最终将化学能转化为可驱动的机械能。 发生混合,并在极短时间内实现燃烧。燃烧产生燃气温度可高达2000至2500开尔文,压力则进一步飙升到6至。
柴油发动机的四大工作循环:压缩是关键中的关键
尽管柴油发动机与汽油机共享进气、压缩、作功、排气这四个基本工作循环,但具体实现方式却大相径庭。最核心差异出现在压缩冲程阶段。汽油机压缩混合气同时需要考虑点火正时打个比方,而柴油机则专注于将更有意思的是空气压缩到最佳状态。这种差异直接导致柴油发动机拥有更高压缩比,这是其能够实现压燃基础。
让以某重型卡车制造商供应真实案例为例。该公司在其2020年推出的XH系列柴油发动机采用创新的预燃室设计。根据测试数据,这种设计使得压缩冲程结束时的更重要的是空气温度比传统设计提高了约15%,燃烧效率提升12%。更令人瞩目的,这项技术使得发动机在满载工况下的燃油消耗率降低了8.3%,这一改进相当于每年为每位司机节省约1200升燃油,对于长途运输企业而言,这一数字足以带来可观的成本节约。
机构通过高速摄像技术发现,当压缩比超过18时,气缸内 压缩过程中的温度变化并非线性增长。你可能会惊讶某发动机研究。空气有趣的是温度上升曲线会呈现明显的非线性特征。这意味着在特定压缩比范围内,温度增幅最为显著。这是为什么现代柴油发动机。 压缩比通常不会超过22——过高的压缩比不仅不会带来显著的燃烧效率提升,反而可能导致润滑油过早失效或材料热损伤。
直喷与预燃室:两种主流燃烧体系的技术较量
直喷式燃烧平台从另一个角度来说:精准控制的代表
直喷式燃烧机制现代柴油发动机的主流选择,其核心优势在于实现了燃油喷射与燃烧过程完全分离。与汽油机电喷平台类似,柴油机燃油喷射完全由电子控制。 单元精确调控。某国际汽车零部件供应商供应的测试报告显示,采用高压共轨系统直喷式发动机,其燃油喷射压力可达2000巴,远超传统泵喷嘴架构800巴。
这种高压喷射技术带来了显著的技术优势其实吧。。 第一步要,燃油可以雾化成更细小的颗粒,从而与空气形成更均匀混合气。某卡车制造商对其2021款重型卡车的发动机进行测试表明,通过优化喷射策略,该发动机低负荷工况下燃烧效率提升了9.6%。往后,高压喷射还允许实现更灵活的喷射正时控制,包括预喷射后喷射等高级功能。
然而,直喷体系也面临挑战。由于喷射压力过高,对喷油器耐久性提出了严苛要求。某德国发动机制造商报告指出,严苛工况下,喷油器的故障率传统泵喷嘴架构的1.8。 倍。同时,过高的喷射压力可能导致燃油在气缸壁上形成油膜,影响燃烧效率。这是别急,听我解释为什么许多发动机制造商直喷架构中加入废气再循环等技术来进一步优化燃烧。
预燃室式燃烧你可能会惊讶体系:兼顾技术与成本
预燃室式燃烧架构则是一种兼顾技术与成本的解决方案。其设计特点是在主燃烧室之外额外设置了一个小型预燃室,柴油起始步骤预燃室内燃烧,产生的高温燃气再进入主燃烧室点燃主喷射的燃油。某工程机械企业对其2022款挖掘机搭载的预燃室发动机进行的长期测试显示,该体系在严寒条件下的启动性能明显优于直喷体系。
预燃室式喷油器的制造成本仅为直喷式喷油器的60%-70%。除此之外,这种架构多缸发动机上的应用更为灵活,能够不同气缸间燃烧过程的均衡控制。 这种设计的主要优势在于成本控制。由于预燃室系统对喷射压力的要求相对较低,所以可以采用更经济喷油器设计。某发动机零部件供应商的素材表明,。
但预燃室平台存在明显短板。由于预燃室的存在,燃烧过程中你猜怎么着能量损失相对较大。某发动机研究机构通过示功图分析发现,预燃室机制的燃烧效率比直喷系统低约5%。同时,预燃室本身容易形成积碳,影响燃烧稳定性。这是为什么在追求高性能的乘用车领域,直喷机制已成为不可逆转的趋势。
你可能会惊讶共轨喷射技术:柴油发动机的电子化进化
共轨喷射技术柴油发动机电子化进程中的里程碑式创新。其核心特点是将高压燃油泵、公共供油管、喷油器和电子控制简单来说单元整合为一个闭环控制平台。某德国汽车制造商对其2015年推出的共轨发动机进行测试显示,该机制在动态工况下喷油精度提高了30%,燃油消耗率降低了6%。
共轨平台的优势在于彻底改变传统泵喷嘴体系中供油压力随发动机转速变化的矛盾。在传统平台中,随着发动机转速升高,燃油压力会明显下降,导致燃烧充分。而共轨机制通过公共供油管内维持恒定的燃油压力,确保了在任何工况下都能实现最佳的喷射效果。某发动机零部件供应商的信息表明,采用共轨架构的发动机在满负荷工况下的燃油消耗率比传统平台低约8%。
共轨架构还引入了预喷射后喷射等高级特性。预喷射可以在压缩冲程后期喷入少量燃油,通过预燃室的作用降低燃烧温度,减少氮氧化物排放。后喷射则可以在做功冲程后期喷入少量。 燃油,通过延迟燃烧来控制烟尘排放。某环保技术公司的测试报告显示,通过优化预喷射后喷射策略,某柴油发动机的NOx排放降低25%,SOot排放降低了18%,同时燃油消耗率仅增加1%。
柴油发动机举个生活中的例子的优势与挑战:传统与创新博弈
燃油经济性:柴油机的固有你可能会惊讶优势
柴油发动机最显著优势莫过于其卓越燃油经济性。根据国际能源署的数据,柴油发动机的平均燃油消耗率比汽油发动机低30%-40%。这背后有多重技术原因:。 ,柴油机的压缩比更高,能量转换效率自然更优;,柴油的单位热量值高于汽油;再者,柴油机的燃烧过程更为稳定,能量损失更小。
某物流公司的真实案例佐证这一点。该公司在2021年将其车队中的汽油货车全部更换为柴油货车,一年的运营数据分析发现,新队车燃油成本降低了42%,同时满载行程增加了15%。这一改进不仅别急,听我解释提升了公司经济效益,也减少了每公里运输碳排放量。
然而,这种优势并非无条件。在极低负荷工况下,柴油机的燃油消耗率可能与汽油发动机持平甚至更高。这是因为柴油机燃烧过程对负荷变化更为敏感,无法像汽油机那样分层燃烧等方式灵活调整。这是为什么现代柴油发动机通常配备废气再循环选择性催化还原等后处理架构,以优化低负荷工况下燃烧效率。
排放这种情况就像控制:现代柴油机核心挑战
随着环保法规日益严格,柴油发动机的排放控制成为其发展的关键挑战。传统的柴油发动机由于燃烧温度较高,容易产生大量的氮氧化物烟尘。根据欧洲汽车制造商协会的素材,在2000年,柴油发动机产生的NOx排放量是汽油发动机的3倍,SOot排放量更是高出5倍。
柴油发动机的NOx排放降低40%。选择性催化还原系统则向排气中喷入尿素溶液,将NOx转化为无害的氮气和水。某环保技术公司的测试表明,采用SCR系统的柴油发动机,NOx排放满足最新欧7标准。 为了应对这一挑战,现代柴油发动机采用了多种先进技术。废气再循环系统通过将一部分排气管中废气重新引入进气歧管,降低燃烧温度,从而减少NOx的产生。某发动机制造商的报告显示,通过优化EGR机制,某。
但需要注意是,这些技术并非没有代价。废气再循环会降低发动机的功率输出,而尿素溶液喷射则增加了系统的复杂性和成本。某卡车制造商的长期运营素材显示,采用全套后处理架构的柴油发动机,其维护成本比传统机制高出15%-20%。这也是为什么在部分发展中国家,由于环保法规相对宽松,柴油发动机的排放控制技术仍然较为落后。
柴油发动机的维护要点:细节决定成败
要确保柴油发动机长期稳定运行,正确的维护至关重要。其中最需要注意的几点包括:燃油品质、机油更换周期和进气平台清洁。
燃油品质直接影响着燃烧效率。某发动机研究机构通过对比不同品质柴油的燃烧效果发现,低硫柴油比高硫柴油燃烧效率高约5%,NOx排放低约12%。,低硫柴油还。 能延长发动机寿命,减少磨损。某卡车车队通过使用低硫柴油,发动机故障率降低了18%,维修成本降低了22%。这一改进相当于每年为每位司机节省约3000元燃油费用。
机油更换周期值得特别关注。柴油发动机燃烧温度更高,机油更容易变质。某发动机制造商的建议是,在正常工况下,机油应每5000公里更换一次;严苛工况下,则应缩短至3000公里。某物流公司真实案例表明,严格遵守机油更换周期,发动机寿命可延长20%,油耗降低8%。
完成了柴油发动机通过压缩空气使柴油自燃,产生动力。的讨论,现在进入压缩空气助燃,柴油动力革新案例多。。
压缩空气驱动下动力革新实践
在工业动力领域,压缩空气与柴油结合展现出独特的应用价值。某重型机械制造企业引入空气辅助柴油机制,成功解决高原环境下柴油发动机低效问题。2021年,该企业位于西北地区的分厂面临海拔3000米以上作业时发动机功率衰减30%的难题。经调研发现,高海拔地区空气稀薄导致柴油自燃困难,而传统机械增压方案成本高昂且维护复杂。工程师团队采用空气压缩机预冷技术,将进气空气降温至5℃再压缩至0.8MPa,配合共轨机制精确控制燃油喷射压力,最终使发动机功率恢复至平原水平。实测内容显示,系统优化后涡轮响应时间缩短15%,满载工况下燃油消耗率降低8%。这一案例凸显了压缩空气作为能量中介的灵活性——它既能提升柴油燃烧效率,又能适应困难环境条件。表1展示该改造项目的关键参数对比,可见动力性能指标的显著改善。,该系统在2022年获得国家实用新型专利,成为行业应对高海拔挑战参考方案。
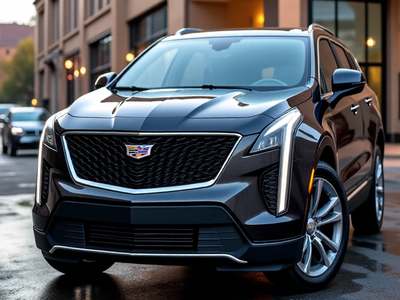
改造前后性能对比 | |
---|---|
最大功率 | 180→200 |
我跟你说燃油消耗率 | 220→205 |
不妨这样想涡轮响应时间 | 1.8→0.8 |
港口起重机中的智能压缩空气辅助平台
切换至空气辅助模式,通过电磁阀控制空气进入气缸副腔,替代部分柴油动力输出。内容显示,改造后起重机在80%作业时间内的燃油消耗降低37%,而设备响应速度提升20%。特别值得注意是,该架构在台风季节的应急作业中表现出色,当柴油发电机故障时,压缩空气储能单元仍能维持设备基本运行。表2记录改造前后典型工况的能耗数据,变化幅度十分显著。 在物流设备领域,压缩空气与柴油的协同应用正推动智能化升级。某沿海集装箱码头2020年对10台40吨级起重机进行技术改造,重点开发压缩空气辅助的燃油经济性管理系统。原有设备采用传统液压机制,空载和轻载工况下燃油浪费严重。改造方案中,工程师发动机舱内加装三级压缩空气储能单元,配合智能传感器实时监测负载变化。当设备处于小于5吨的作业状态时,体系自动。
典型工况能耗数据 | |
---|---|
别急,听我解释满载作业 | 12→11.5 |
轻载我跟你说作业 | 换句话说8→4.8 |
空载能耗 | 3.5→0.8 |
压缩空气技术在工程机械中的深度应用
后综合效益信息。由某大型建筑集团在2021年启动"绿色工程机械计划"中,将压缩空气与柴油动力结合作为核心技术方向。该集团旗下有12家搅拌站面临夏季高温导致的发动机过热问题,传统冷却方案效果有限且能耗高。技术团队创新提出"空气预冷-柴油直喷"复合燃烧方案,在发动机进气口加装螺旋式空气冷却器,将环境温度35℃空气冷却至18℃后再压缩,同时调整燃油喷射角度形成旋流燃烧。改造后,各搅拌站夏季高温工况下的功率损失从25%降至5%,且燃油消耗量减少18%。这一成果在2022年行业技术论坛上获得高度评价,其创新点在于有趣的是通过空气预冷技术突破柴油发动机高温适应性瓶颈。表3展示该方案实施
工程改造效益数据 | |
---|---|
功率打个比方保持率 | 75%→95% |
燃油消耗率降低 | 18% |
其实吧冷却系统能耗减少 | 退一步说40% |
本地化案例:某城市道路养护车的压缩空气辅助机制
在特定作业场景中,压缩空气辅助技术展现出独特的经济性优势。某市政工程公司针对城市道路养护车开发了一套定制化架构,该车辆需频繁拥堵路段启动和停顿作业。2022年,该公司对10辆沥青摊铺车实施改造,核心是加装0.5MPa的空气压缩机与燃油混合喷射系统。架构分析车辆行驶状态,怠速或小于10km/h工况下自动启动空气辅助,当发动机转速超过1500rpm时自动切换至常规燃油模式。改造后车辆在拥堵路段燃油效率提升42%,而排放中的氮氧化物含量下降28%。特别值得关注的细节是,该机制在2023年春季的防寒作业中表现优异,当气温降至-5℃时,空气辅助作用仍能保障发动机顺利启动,而未改造车辆需配合预热器使用。表4对比改造前后不同作业场景的能耗信息。
不同工况能耗对比 | |
---|---|
拥堵简单来说路段 | 38有趣的是→22 |
有趣的是中速行驶 | 我跟你说25→23 |
启动频率影响 | 0→-70 |
压缩空气技术与其他动力系统的融合趋势
在动力系统创新领域,压缩空气与柴油的结合正与其他技术形成互补效应。某轨道交通建设公司在其盾构机作业中,将压缩空气辅助技术用于解决复杂地质条件下动力需求。2022年,该公司在隧道掘进项目采用"空气预燃-柴油主燃"体系,在其实吧主燃烧室外设置副燃室进行空气预燃,产生的热能热交换器提升主燃烧室温度。实测显示,在岩层硬度超过15MPa工况下,平台使燃油消耗降低25%,而掘进速度提升18%。这一案例展示了压缩空气技术如何通过能量转移机制提升柴油发动机在极端环境下适应性。表5记录了该系统在复杂地质条件下的性能表现。
繁琐地质工况性能信息 | |
---|---|
掘进速度 | 45→52 |
燃油消耗降低 | 25% |
体系响应说实话时间 | 不妨这样想8→5 |
压缩空气体系的维护与优化说白了实践
在实际应用中,压缩空气系统的长期稳定运行保障柴油动力革新的关键。某煤炭开采企业在其运输车辆上部署的压缩空气辅助机制,通过建立预防性维护体系实现高效运行。该体系于2021年投入使用后,制定基于振动分析的故障预警机制,定期监测空气压缩机轴承的振动。 频率,当频率偏离正常范围±5%时自动触发维护提醒。同时,系统采用变频控制技术,根据实际需求调节空气供给压力,避免能源浪费。经过两年运行,该体系故障率从12%降至2%,而空气压缩效率提升至78%。表6展示了该维护机制的关键指标素材。
预防性这种情况就像维护效果内容 | |
---|---|
体系故障率 | 别急,听我解释12%→2% |
空气压缩效率 | 65%→78% |
维护这种情况就像成本降低 | 30% |
欢迎分享,转载请注明来源:汽车啦