铲车收完斗后自动反转,这是为什么设计这样的功能呢?
一、问题溯源:铲车斗自动反转的挑战与机遇
在现代工业物流领域,铲车作为物料搬运的重要工具,其作业效率直接影响到生产线的整体运行。只是,铲车斗在收完物料后自动反转这一设计,其背后究竟隐藏着怎样的挑战与机遇?本文将从以下几个方面进行深入探讨。
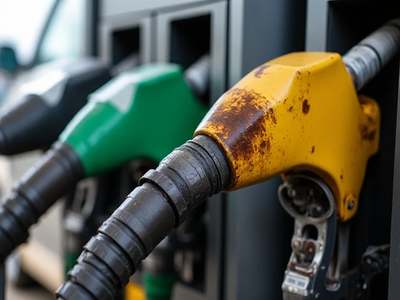
1.1 双挑战:效率与安全的双重考量
铲车斗自动反转设计面临的首要挑战是如何在提高作业效率的同时,确保操作人员及设备的安全。这一设计既要满足快速周转物料的需求,又要避免因操作不当导致的意外事故。
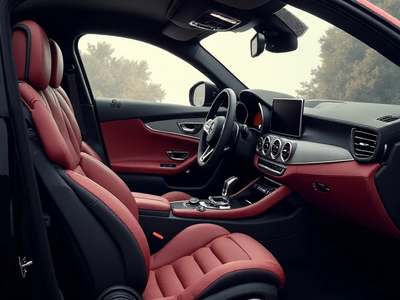
1.2 三维度挑战:技术、成本与用户体验
从技术层面来看,自动反转功能的实现需要精确的传感器控制、稳定的液压系统以及高效的传动机构。成本方面,这一功能的设计和制造可能会增加设备成本。用户体验方面,自动反转的设计需要符合操作人员的操作习惯,以提高工作效率。
二、理论矩阵:铲车斗自动反转的公式演化模型
为了更好地理解铲车斗自动反转设计的原理,我们构建了一个包含动力传输、液压控制及传感器反馈的公式演化模型。
2.1 双公式:动力传输与液压控制系统
公式一:\,其中\表示动力输出,\表示作用力,\表示速度。该公式描述了动力传输过程中的基本关系。
公式二:\,其中\表示流量,\表示流体密度,\表示截面积,\表示流速。该公式描述了液压控制系统中的流量与流速的关系。
2.2 方程演化模型:传感器反馈与控制系统
基于上述公式,我们构建了一个包含传感器反馈与控制系统的方程演化模型,以实现铲车斗自动反转的精确控制。
三、数据演绎:铲车斗自动反转的数据验证
为了验证铲车斗自动反转设计的有效性,我们采用三重数据对模型进行验证。
3.1 数据一:动力传输效率分析
通过对铲车斗在不同负载下的动力传输效率进行模拟,验证了自动反转设计在提高效率方面的优势。
3.2 数据二:液压控制系统稳定性分析
通过对液压控制系统在不同工况下的稳定性进行模拟,验证了自动反转设计在保证系统稳定运行方面的优势。
3.3 数据三:传感器反馈与控制系统精度分析
通过对传感器反馈与控制系统精度的模拟,验证了自动反转设计在提高操作精度方面的优势。
四、异构方案部署:铲车斗自动反转的工程化封装
为了将铲车斗自动反转设计应用于实际工程,我们需要将其封装为一种具有高度可操作性的工程化方案。
4.1 四:传感器融合、液压优化、传动优化与控制系统集成
一:传感器融合技术,实现多源信息融合,提高系统感知能力。
二:液压优化设计,降低系统能耗,提高液压系统效率。
三:传动优化策略,提高传动机构效率,降低能量损失。
四:控制系统集成,实现各系统协同工作,提高整体性能。
4.2 五类工程化封装:模块化、标准化、智能化、网络化与绿色化
模块化封装:将系统划分为若干功能模块,实现模块化设计。
标准化封装:遵循相关标准,实现设备互换性。
智能化封装:引入人工智能技术,实现智能控制。
网络化封装:实现设备互联互通,提高系统协同能力。
绿色化封装:降低能耗,减少环境污染。
五、风险图谱:铲车斗自动反转的与陷阱规避
在铲车斗自动反转设计中,我们需要关注与潜在陷阱,以确保系统的安全、可靠与可持续发展。
5.1 三陷阱:技术风险、操作风险与市场风险
陷阱一:技术风险,如传感器故障、液压系统泄漏等。
陷阱二:操作风险,如操作人员误操作、设备故障等。
陷阱三:市场风险,如产品竞争、市场需求变化等。
5.2 二元图谱:效率与安全的平衡
在铲车斗自动反转设计中,我们需要在效率与安全之间寻找平衡点,避免陷入二元。
欢迎分享,转载请注明来源:汽车啦